Inside the world of wind turbine blade repair – part 1
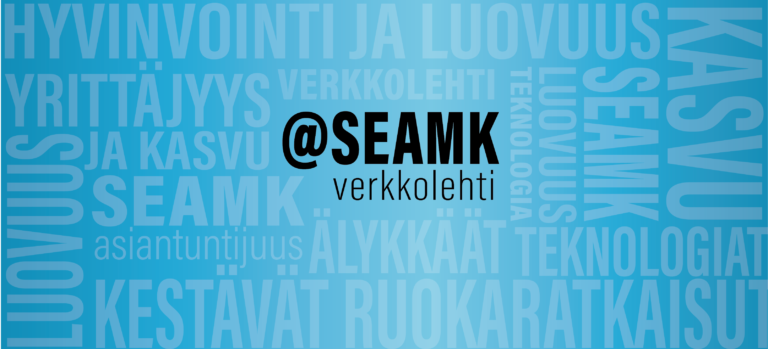
Wind energy is one of the fastest-growing renewable energy sources, and as a result, the demand for skilled professionals in this field has been on the rise. In this two-part article series, we share our firsthand experience during a specialized training session focusing on wind turbine blade repair held in Vaasa, Finland. This part focuses on the foundational knowledge required in the field including career overview, safety protocols, and the intricate process of repair.
A few words about the WIND project itself. The project has been funded by the European Union’s Recovery and Resilience Facility (RRF), which is the key instrument of the EU’s Recovery Facility (NextGenerationEU). The financing has been granted by the Service Centre for Continuous Learning and Employment (SECLE). The Service Centre promotes the competence development of working-age people and availability of skilled labour. The operations of the Service Centre are overseen by the Ministry of Education and Culture and the Ministry of Economic Affairs and Employment.
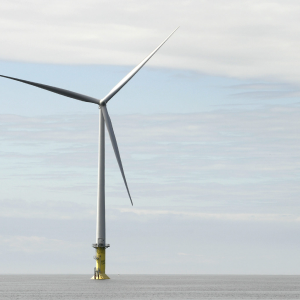
Career Overview
The role of a wind turbine blade repair technician is one of the highest-paying technician jobs, with entry-level positions offering wages as high as 25 euros per hours. However, like any other job, this career comes with its own set of benefits and risks. As a result, a good blade repair technician must know how to work safely, using proper personal safety equipment (PPE) and must possess the skills to mitigate the risks and hazards associated with each repair task. In addition, aspiring technicians must also be medically fit as this role can be so demanding. In theory, the certification for blade repair technicians does not typically have an expiration date if the technician remains actively performing tasks such as repair and inspection in the field.
As part of the SEAMK and SEDU Wind Project initiative, we had the opportunity to attend a specialized training session on wind turbine blade repair procedures in Vaasa. Few career paths require such a steep accumulation of experience to excel. The role of a wind turbine blade repair technician is one of the most demanding career paths, requiring immense determination and courage. We were truly impressed by the professionalism and extensive knowledge of the instructor, who has accumulated more than 20 years’ experience in the field. His expertise made the job of a wind turbine blade repair technician seems almost routine. No wonder Bladefence is considered one of the best in the field, with a reputation for delivering quality service to customers in Finland, Sweden, Denmark, Estonia etc., covering most of the Nordic and Baltic regions.
The Instructor and Training Overview
The training took place at Bladefence’s new warehouse operations office in Vaasa, Finland, and was led by one of Bladefence employees, who is also a Quality and Composite Specialist at Bladefence. The instructor, a former blade repair technician himself with over 15 years’ experience, provided a detailed overview of blade repair process. The day’s training was divided into stages, each demonstrating a different aspect of repairing a wind turbine blade.
He emphasized the benefits of understanding the design of wind turbines and blades which often helps technicians determine the number of layers, fibre orientation and materials at different points along the radius of the blade.
Personal Protective Equipment (PPE) and Safety
One of the primary concerns for blade repair technicians is safety. As a result, the instructor provided an in-depth look at the personal protective equipment required for blade repair work. Essentially, these items include gloves, shoes, gear, masks etc. During the training, we were each given the opportunity to test out the gear, ensuring that all parts were properly aligned and fasten for maximum comfort and effectiveness. The gear is available in different sizes, allowing for a proper fit tailored to everyone’s body.
Additionally, he discussed the safe handling of chemicals used in repair work such as resin and hardener. He stressed the importance of understanding the health risks associated with these materials and how to prevent accidents caused by improper handling.
Blade Construction and Repair Techniques
The instructor covered several topics, including blade construction, components, materials and aerodynamics. Another thing that was mentioned was how to use blade radius measurements to pinpoint specific areas for damage inspection. For example, these measurements can serve as reference points for assessing the condition of the blade and identifying potential faults.
Common blade damages include erosion, delamination, cracks, foreign object collisions, and mishandling during transportation to wind farm from the factory. In some cases, temporary repairs are made to prevent further damage before final repairs are carried out. Final repair typically involves using appropriate materials in the right weather conditions and may include grinding, lamination, and leading-edge protection.
He also introduced and explained the reinforcement materials used in blade repairs, such as glass fibre, carbon fibre, unidirectional (UD) fibre, Biaxial (biax) fabric and Triaxial (triax) fabric materials.
Repair Process
The first step in the blade repair process is damage assessment. During this phase, the blade is inspected to determine the extent of damage. This often involves a variety of inspection methods, such as visual inspection, thermal imaging, ultrasonic testing, or drone inspection. The results of the damage assessment help determine the quantity of resin required for the repair, which can then be used to calculate the amount of other materials needed.
The next step is the surface preparation, which involves thorough cleaning of the damaged area to remove dirt, debris, or loose materials. In some cases, sanding or grinding of the surface may be necessary to ensure a smooth and clean surface for easy bonding of the repair materials.
Following surface preparation, the next step is material selection. The choice of materials depends on the type and extent of the damage, the material of the blade, and the size of the affected area. In this training, the materials used included resin, hardener, UD fabric, and biaxial fabric. Resin serves as both an adhesive and a matrix for the composite repair. Hardener is mixed with the resin to provide strength and initiate curing. The ratio of resin to hardener is determined based on the manufacturer’s specifications. The quantity of resin is calculated based on the size and extent of the damage, while the UD and biax fiberglass sizes are determined by the dimensions of the damaged area. Typically, UD fabric is applied to cover the entire damaged area and should extend a few centimetres beyond the damage to ensure proper bonding. Similarly, biax fabric is cut into specific shapes to fit the repair area and is laid with sufficient overlap to reinforce the blade.
The layering step involves applying multiple layers of UD and biax fabrics over the damaged area. The materials are aligned and oriented properly to provide the necessary structural strength and reinforcement for the blade. Depending on the nature of the repair, the number of layers can vary, from just a few to several layers. Each layer is impregnated with the resin and hardener mixture to bond the materials together.
The final step in the process is curing, which allows the resin to harden under controlled conditions. During this step, a process known as vacuum bagging was performed. This process involves inserting a vacuum hose around the perimeter of the layers. The layers are then covered with a plastic bag, and all edges are well sealed to prevent the possibility of air leak. The purpose of vacuuming is to remove air bubbles that are trapped between layers, enhance resin distribution, create a negative pressure that compresses the layers together tightly and ensure proper resin penetration.
Also, heat or UV light may be used to accelerate the curing process and ensure the repair is completed properly. In our case, a heat blanket is used to cover the composite to accelerate curing reaction. The other benefit of this includes provision of uniform temperature across all layers thereby minimizing the risk of uneven curing. The heat can slightly reduce resin’s viscosity thereby promoting better flow.
Oriyomi Oladele
Project Worker
B.Sc. (Physics), B.Eng. (Information Technology)
SEAMK
Essi Hauta
Expert, RDI
M. A. (Education)
SEAMK
References
Bladefence Europe. https://www.bladefence.com/
Global Wind Organisation. https://www.globalwindsafety.org/
Blade Repair Training Standards. https://assets-global.website-files.com/5ce6247122f44f2bd5edebbe/60180bf0556ad8e125ece736_2020-10-01_BR_V1.1.pdf
Wind Turbine Inspection: A Guide. https://www.flyability.com/blog/wind-turbine-inspection
Wind Turbine Inspection & Repair. https://www.nordicaccess.fi/en/wind-turbine-maintenance
Suomen uusiutuvat ry: Materiaalipankki. https://suomenuusiutuvat.fi/yhdistys/materiaalipankki/