SeAMKin konetekniikan laboratoriosta kamiinoita Ukrainaan
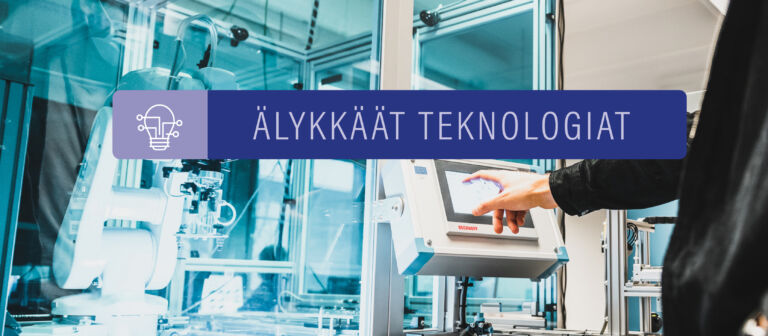
Lappeenrannan-Lahden teknillisen yliopiston kamiina-projektin uutisointi YLE:llä herätti SeAMKilaiset (https://yle.fi/a/74-20006882). Ukrainan kriisi toki on ollut tiedossa ja kahvipöytäkeskusteluissa pitkään, ja erilaista avustustoimintaa on henkilöstön toimesta harjoitettu aikaisemminkin. Uutisoinnin myötä herättiin toimimaan myös kamiinatuotannon parissa. Laboratoriossa ei kuitenkaan kamiinatuotannon vaatimaa materiaalia ollut vaan materiaalien suhteen käännyttiin yhteistyökumppaneiden puoleen. Prima Power -konserniin kuuluvalta Finn-Power Oy:ltä saatiin kamiinan pääasiallisena materiaalina olevaa 3 mm:n teräslevyä, levyt saapuivat laboratorioon ja tuotanto saattoi alkaa.
Kamiinatuotannossa on useat konepajatuotannon elementit
LUT-yliopisto jakaa kamiinaa koskevilla verkkosivuillaan (https://www.lut.fi/fi/kamiina) vapaasti käytettäväksi ja muokattavaksi kamiinan valmistuspiirustukset .dxf ja .pdf tiedostomuodoissa. Piirustusten pohjalta päästiin verrattain suoraviivaisesti käynnistelemään tuotantoa, joka aloitettiin luomalla levytyökeskukselle leikkausohjelma. Tässä nestausprosessissa käytännössä tehdään materiaalihukan näkökulmasta tärkeimmät ratkaisut. LUTin piirustusten yksi vahvuus oli se, että materiaalihukka voitiin minimoida helpohkosti. Alla olevissa kuvissa 1 tuotanto ollaan käynnistämässä, vasemmalla nestataan leikkausta ja oikealla nostetaan ensimmäistä levyä levytyökeskukseen. Kuva 1. Aluksi LUT-yliopiston dxf-kuvien perusteella nestataan levyleikkaukset levytyökeskukselle (vas.). Seuraavaksi nostetaan ensimmäinen levy leikkaukseen. SeAMKin konetekniikan laboratoriossa on levytyökeskuksena Finn-Powerin valmistama yhdistelmälevytyökeskus, jolla 3 mm:n teräslevyn laserleikkaus on hyvin suoraviivaista (kuva: Pasi Junell).
Osien leikkaamisen jälkeen on tuotannon seuraavassa vaiheessa niiden särmääminen muotoonsa. LUTin suunnitteleman kamiinan tuotannossa särmäystä on melko paljon, ja erityisesti tulipesän pohjaosan särmäys asettaa SeAMKin särmäyspuristinta käytettäessä hieman haasteita. Pohjaosassa on kaksi sellaista taittoa, joihin konetekniikan laboratorion särmäyspuristimen takavasteen käyttö on mahdotonta. Lisäksi pohjaosaa on tarpeen kääntää taittojen välillä. Tämä aiheuttaisi mittavammassa tuotannossa ergonomiahaasteita, ja lisäksi kuluttaa tarpeettomasti aikaa ja lisää lopputuotteeseen mittavirheen mahdollisuutta. Nyt tehdyssä sarjassa kappalemäärä on kuitenkin niin pieni, ettei tähän nähty tarpeelliseksi tehdä muutosta. Joka tapauksessa nämä haasteet ovat suunnittelun kannalta hyvin opettavaisia.
Kuva 2. Teräslevyjen leikkauksen jälkeen on seuraavana työvaiheena osien särmääminen muotoonsa. Särmäysohjelman teko (vas.) toteutettiin kiireisen aikataulun vuoksi manuaalisärmäykseksi (oik.) (kuva: Pasi Junell).
Osien leikkauksen ja särmäämisen jälkeen tuotannossa on seuraavaksi kokoonpanon hitsaaminen ja kokoaminen. Erityisesti tulipesän osalta hitsauksen robotisointi oli tarpeen, ja muutenkin opettavainen työvaihe. LUTin toimittamissa piirustuksissa ei ollut tarjolla kokoonpanokuvaa, joten robotisoinnin ensimmäisessä vaiheessa piti levyleikkauskuvien pohjalta tällainen tehdä. Sen jälkeen luotiin hitsauksen ohjelma konetekniikan laboratorion hitsausrobottiaseman digitaaliseen kaksoseen. Lopulta tulipesän hitsaus sitten toteutettiin robotisoidusti. Kuvassa 3 on esillä vasemmalla ohjelman testaus digitaalisessa kaksosessa ja oikealla sama ohjelmakohta varsinaisessa robottisolussa. Hitsauksesta tullaan julkaisemaan myös video Youtubessa.
Hitsaukseen jäi myös manuaalista hitsaamista. Esimerkiksi kamiinan jalkojen paikoittaminen vaatisi robottihitsaukseen sellaisen hitsausjigin, että sen tuottaminen ja hitsausohjelman luonti olisi ollut näin pienessä sarjatuotannossa paljon työllistävämpää kuin itse hitsauksen tekeminen. Oppimisen kannalta jalkojenkin hitsauksen automatisointi olisi tietysti ollut paikallaan, mutta tuotannon aikajänne ei tällä kertaa siihen oikein antanut myöden. Vastaava tilanne oli kamiinan luukun suhteen.
Kuva 3. Tulipesän hitsaus robotisoidusti. Hitsausohjelma tuotettiin ja testattiin ensiksi robottisolun digitaalisessa kaksosessa (vas.) ja tämän jälkeen siirrettiin varsinaisen robottisolun tehtäväksi (oik.) (kuva: Pasi Junell).
Tuotannon kokonaisuudesta
Tätä artikkelia kirjoitettaessa on kulunut jokseenkin tarkalleen kaksi viikkoa siitä, kun SeAMKissa päätettiin osallistua kamiinoiden tekemiseen LUT-yliopiston piirustusten mukaan. Kamiinoiden tuotanto vaikuttaa puhuttelevan suomalaisia ja myös eteläpohjalaisia. Kiinnostusta materiaalilahjoituksiin oli laajemminkin, vaikka tähän ensimmäiseen sarjaan SeAMKin tuotannossa ehdittiin ottaa mukaan Finn-Powerin lahjoittamat ohutlevyt ja Finnish Oren lahjoittamasta putkesta valmistetut hormisovitteet. Myös tuotantoon osallistuneet opiskelijat ja henkilöstön jäsenet kokivat tekevänsä merkityksellistä työtä, ja työn tarmo oli sen mukaista. Tällaisen piensarjan tuottaminen on myös ollut hyvä oppimiskokemus sekä opiskelijoille että henkilökunnalle. SeAMKin näkökulmasta tuotanto sijoittui kiireiseen aikaan. Syyslukukauden viimeisellä viikolla on tietysti opiskelijoilla opintojaksojen tenttiajat, mikä kuormittaa sekä opiskelijoita että henkilöstöä. Tästä huolimatta on saatu tuotetuksi 20 kappaletta kamiinoita. Niin kamiinoiden suunnittelussa kuin niiden tuotannon toteutuksessa on parannettavaa, mutta aikataulu oli verrattain tiukka, jotta kamiinat saatiin valmiiksi ennen joulun aikaa. Viikko 50 oli opiskelijoiden viimeinen läsnäoloviikko, ja se muodosti siten luonnollisen aikarajan tuotannolle. Nyt tehtyä sarjaa voi luonnehtia ikään kuin teollisuudessa tuotannon esisarjaksi. Kamiinat toimittaa eteenpäin Ukrainaan Omri ry:n vapaaehtoistyöntekijät.
Kuva 4. LUT-yliopiston verkkosivuilta vapaasti ladattavat piirustukset (vas.) muodostivat SeAMKin kamiinatuotannon lähtökohdan. Piirustuksia muokattiin hieman konetekniikan laboratorion kannalta paremmin tuotantoon sopiviksi. Kuitenkin pääpiirteittäin kamiina on samanlainen kuin LUTin valmistamat kamiinat. Keskellä ylhäällä on nähtävissä ensimmäinen prototyyppi. Tämän jälkeen tuotettiin Finn-Powerin lahjoittamista teräslevyistä 20 kamiinan sarja (oik.) (kuva: Pasi Junell).
Pasi Junell
Lehtori
SeAMK Konetekniikka