Sulfidipohjaiset kiinteäelektrolyyttiset akut – ratkaisu vai vain yksi este matkalla?
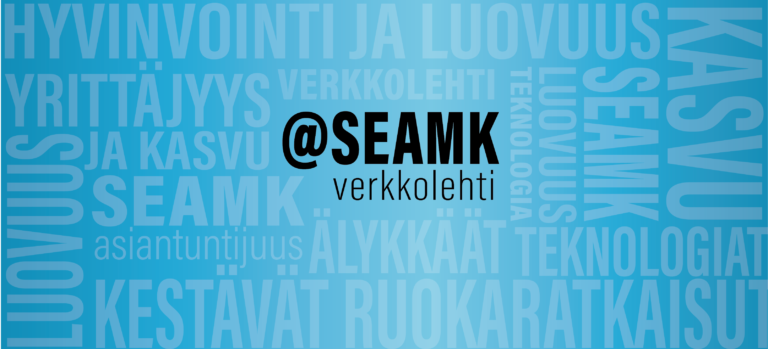
Kiinteäelektrolyyttisiä akkuja (solid-state batteries, SSB) on pidetty energiavarastoinnin Graalin maljana jo vuosikymmenten ajan. Niiden on luvattu tuovan markkinoille suuremman energiatiheyden, paremman turvallisuuden ja nopeamman latauksen kuin perinteiset litiumioniakut. Vaikka läpimurtoja on tapahtunut, kaupallistaminen on edelleen kesken. Nyt katseet kohdistuvat sulfidipohjaisiin elektrolyytteihin, joiden sanotaan johtavan kehitystä. Ovatko ne vihdoin ratkaisu vai vain yksi välietappi matkalla kohti toimivia kiinteäelektrolyyttisiä akkuja? Tässä artikkelissa pureudutaan teknologisiin, valmistukseen liittyviin ja rajapintoihin kytkeytyviin haasteisiin, jotka määrittelevät sulfidien tulevaisuuden.
Kosteusherkkyys: ratkaistavissa, mutta kalliilla hinnalla
Sulfidielektrolyytit reagoivat rajusti kosteuden kanssa, muodostaen myrkyllistä rikkivetyä (H₂S) selvä punainen lippu massatuotannossa. Kuitenkin moderneissa litiumioniakkujen tuotantotiloissa ylläpidetään jo nyt erittäin kuivaa ympäristöä (<1 % suhteellinen kosteus) hygroskooppisten materiaalien, kuten elektrolyytin, käsittelyyn. Näin ollen vastaavien olosuhteiden luominen sulfidien tuotantoon on täysin tehtävissä ja mahdollista, mutta kyllä jonkun pitää tämä lysti myös maksaa. Vaikka oksidit ja polymeerit kärsivät vähemmän kosteusherkkyydestä, sulfideilla on selvä etu ionien johtavuudessa (10–2–10–3 S/cm vs. oksidien 10–6 S/cm). Tämä tekee niistä houkuttelevan vaihtoehdon erityisesti sähköautoihin, joissa suorituskyky ratkaisee.
Kemiallinen vakaus: rajapintojen-illuusio
Ensimmäiset tutkimukset väittivät sulfideja vakaiksi, mutta myöhemmät analyysit paljastivat niiden ja litium-metallianodin välillä tapahtuvaa rajapintadegeneraatiota. Esimerkiksi LG Energyn kokeet osoittivat, että Li₂S kerrostuu anodin ja elektrolyytin rajapintaan, kasvattaen vastusta ajan myötä. Ratkaisuja, kuten atomikerroskasvatettuja (ALD) LiNbO₃-pinnoitteita ja muita lisäaineita, kehitetään ongelman hillitsemiseksi, mutta epäselvyys säilyy: onko järjestelmä täysin kiinteä vai piileekö siinä yhä pieniä määriä nestemäistä elektrolyyttiä? Esimerkiksi startup-yritys QuantumScape on avoimesti myöntänyt käyttävänsä “hybridimalleja”, joissa katodi muistuttaa enemmän hammastahnaa kovan kiinteän aineen sijaan. Ennen kuin täydellinen kiinteä kiinteän rajapinta saavutetaan, sulfideihin saatetaan edelleen suhtautua vain “puolikiinteinä” välivaiheina.
Litiumin rajapinta: tasapainon löytäminen
Litium on kemiallisesti aggressiivinen ja aiheuttaa helposti latauksen aikana dendriittien kasvua ja mekaanista rasitusta sulfidielektrolyyteissä. Uusia ratkaisuja kehitetään jatkuvasti, kuten Toyotan Li₃PS₄-Li₂S-P₂S₅-komposiittielektrolyytti ja Samsungin grafeeni-välikerrokset, jotka auttavat tasaamaan ionivirtausta ja vähentämään dendriittien muodostumista. Samaan aikaan MIT:n “anodittomat” akut pyrkivät poistamaan rajapintaongelmat kokonaan, saostamalla litiumia suoraan virrankeräimeen. Näillä tekniikoilla on onnistuttu pidentämään akkujen käyttöikää noin 1 000 sykliin 80 % kapasiteetilla, mikä on jo lähellä sähköautoakkujen tavoitteita. Pitkäaikaiset hajoamismekanismit, kuten tyhjien tilojen muodostuminen latauksen ja purkauksen aikana, vaativat kuitenkin vielä lisää tutkimusta. Se, kuka ensimmäisenä kehittää toimivan monikerrospinnoitestrategian, voi määritellä alan tulevaisuuden.
Miksi sulfidit ovat ohittamassa oksidit?
Sulfidielektrolyyttien vahvuudet voidaan tiivistää kolmeen pääkohtaan:
Litiumionien johtavuus: Sulfidit (esim. Li₁₀GeP₂S₁₂, 12 mS/cm) yltävät nestemäisten elektrolyyttien tasolle, mahdollistaen jopa 15 minuutin pikalatauksen. Oksidit (esim. LLZO, 0.3 mS/cm) jäävät tästä selvästi jälkeen.
Valmistuksen skaalautuvuus: Sulfidit voidaan sinteröidä alle 300 °C lämpötilassa, kun taas oksidit vaativat yli 1 000 °C, mikä nostaa energiakustannuksia merkittävästi. Esim. BMW:n ja Solid Powerin kumppanuus hyödyntää tätä rullalta rullalle -valmistusmenetelmässä.
Elektrodien yhteensopivuus: Sulfidien mekaaninen pehmeys mahdollistaa noin 90 %:n rajapintakontaktin, kun oksideilla luku on vain 50 %. Esimerkiksi Panasonicin 4 Ah -prototyypit ovat jo saavuttaneet 400 Wh/kg energiatiheyden, joka on noin 100–150 Wh/kg enemmän kuin nykyisten parhaiden litiumioniakkujen energiatiheys.
Tästä huolimatta sulfidien paineenkesto (>50 MPa) on edelleen oksidijärjestelmiä heikompi, mikä on kriittinen ongelma autojen massatuotannossa.
Milloin kaupallistaminen tapahtuu? Ennen 2030-lukua?
Teollisuus investoi valtavasti kehitykseen: CATL suunnittelee pilottituotantolinjaa vuodelle 2027, ja SES AI tähtää hybridisulfiidijärjestelmiin sähköautoille jo vuonna 2026. Kuitenkin rajapintadegradaation ratkaisemattomat haasteet ja korkeat materiaalikustannukset (esim. Li₁₀GeP₂S₁₂ maksaa ~200 €/kg vs. normaali elektrolyytti n. ~15 €/kg) hidastavat laajamittaista käyttöönottoa. Skeptisyys elää kuitenkin edelleen. Bosch esimerkiksi vetäytyi kiinteäelektrolyyttisten akkujen kehityksestä vedoten “vuosikymmenten aikajänteeseen”. Avainasemassa on rajapintojen stabilointi ilman nestemäisiä jäänteitä sekä sulfidisynteesin kustannustehokkuuden parantaminen, esimerkiksi korvaamalla germanium edullisemmilla materiaaleilla. Joten materiaalikemistejä yhä tarvitaan!
Lopputulos: varovaista optimismia
Sulfidipohjaiset kiinteäelektrolyyttiset akut eivät ole mikään taikaratkaisu, mutta eivät myöskään pelkkä kangastus. Ne tarjoavat suhteellisen lupaavan polun turvalliseen ja energiatehokkaaseen akkukehitykseen, mutta onnistuminen riippuu rajapintojen optimoinnista ja tuotantokustannusten alentamisesta. Vaikka vuoden 2030 kaupallistamistavoite voi olla realistinen, varhaisia sovelluksia voidaan nähdä jo esimerkiksi kulutuselektroniikassa tai esim. avaruusteollisuudessa, joissa akun yksikkökustannus on matalampi tai sillä yksinkertaisesti ei ole väliä, ja täten kustannukset eivät ole yhtä kriittisiä kuin sähköautojen massamarkkinoilla. Itse olen monta kertaa sanonut, että kiinteät elektrolyytit ovat aina 5 vuoden ja fuusioenergia aina 50 vuoden päässä. Nyt kuitenkin alkaa pikkuhiljaa tuntua, että tämä ainainen 5 vuotta alkaa pikkuhiljaa kulua.
Juho Heiska
TkT, tutkimus- ja kehittämispäällikkö
SeAMK
Kirjoittaja on väitellyt akkututkimuksen alalta ja kerännyt jo paljon kokemusta kestävään siirtymään liittyen erityisesti energiatekniikan näkökulmasta. Tällä hetkellä hän toimii SeAMKissa digitaalisaatio ja älykkäät teknologiat -tiimissä tutkimus- ja kehittämispäällikkönä.