Akut ovat kuivia
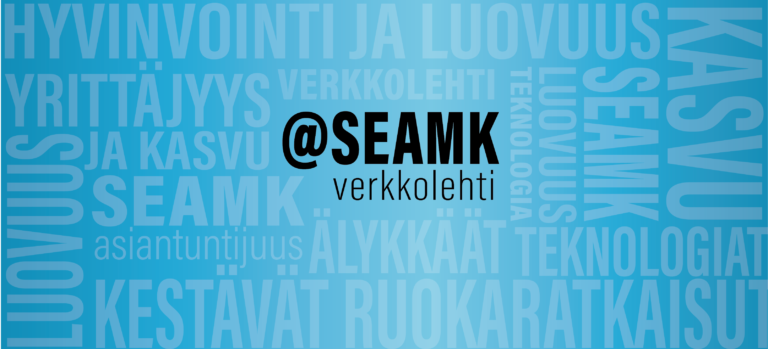
Viimeisimmät edistysaskeleet akkukennojen valmistuksessa ovat varsin kuivia. Benchmark Mineralsin tuore artikkeli kuivaelektroditekniikasta tarjoaa katsauksen ratkaisevaan muutokseen, joka voi mullistaa akkutuotannon kustannusrakenteen ja tiputtaa halpoja hintoja entisestään.(Revolutionising Battery Production, 2024) Akkukennot valmistetaan yleensä seuraavasti (kuva 1): Aluksi valmistetaan anodi ja katodi ‘slurryt’, eli elektrodipastat, jotka päällystetään metallifolioiden päälle. Pastassa oleva ylimääräinen nestemäinen liuotin pitää kuivata ja kerätä talteen, ennen kuin akkukenno voi siirtyä eteenpäin. Tämän jälkeen elektrodit leikataan sopivaan kokoon ja kootaan kennoksi yhdessä erottimen kanssa. Lopuksi kenno täytetään elektrolyytillä ja suljetaan ilmatiiviisti. Akkutuotannossa elektrodislurryn kuivaaminen ja liuottimen talteen kerääminen on perinteisesti ollut tilaa vievä ja kallis vaihe. (Liu ym., 2021) Jos voisimme valmistaa akkuja ilman, että meidän tarvitsee tätä liuotinta kuivata, olisivat säästöt selviä. Kuivaelektroditekniikkaan siirtyminen ei ainoastaan vähennä käyttökustannuksia, vaan myös yksinkertaistaa logistiikkaa ja pienentää ympäristökuormaa, sillä liuottimia ei tarvita. Tämä ei vain vapauta tuotantotilaa, vaan myös säästää energiaa ja vähentää sitä kautta tuotannossa syntyviä päästöjä.
Kuva 1. Pelkistetty kuva akkukennotehtaan toiminnasta. (” Battery Making at a Glance – Battery LAB”, 2023)
Kuivaelektrodit: uusi suunta akkutuotannossa
Kuivaelektrodien valmistus on saanut merkittävää nostetta erityisesti Teslan kaltaisten suurten toimijoiden ansiosta, jotka ovat olleet edelläkävijöitä kuivamenetelmien kehittämisessä. Tesla käyttää kuivaelektroditekniikkaa 4680-kennoissaan, ja heidän kokemuksensa tällä alalla on herättänyt kiinnostusta myös muissa yrityksissä. Tie oli kumminkin pitkä ja kivinen, jotta kuivaelektroditekniikka saatiin toimimaan molemmilla elektrodeilla. (Giesige, 2024) Kuivaelektroditekniikka eliminoi perinteisen jugurttimaisten pastan, mikä tarkoittaa, että monimutkaista ja aikaa vievää kuivausvaihetta ei enää tarvita. Tämän myötä säästetään valtavasti pääomaa ja energiaa, koska tuotantoprosessi tehostuu huomattavasti. Vaikka kuivamenetelmässä on aiemmin ollut teknisiä haasteita, kuten materiaalin tasaisen jakautumisen varmistaminen elektrodipinnoilla ja kalanteroinnin haasteet, näyttää siltä, että nämä ongelmat on nyt ratkaistu onnistuneesti, ja kuivamenetelmä on valmis laajempaan käyttöön akkuteollisuudessa.
Toinen tapa: elektrodislurryn jättäminen pastamaiseen muotoon
Kuivaelektroditekniikan rinnalla on elänyt myös toinen lupaava vaihtoehto, jossa päällystettävä elektrodiseos jätetään enemmän pastamaiseen muotoon. Tämäkin menetelmä mahdollistaa kuivausvaiheen ohittamisen, mikä tarjoaa kustannustehokkaan vaihtoehdon, mutta tuo luonnollisesti omat insinöörihaasteensa. Yritykset, kuten FREYR yhdessä 24M:n kanssa, ovat edistäneet tätä lähestymistapaa, ja alkuvaiheen tulokset olivatkin lupaavia, koska nämä akut olisivat voineet toimia hyvin isoissa akkuvarastoissa. Märkänä rättinä kuitenkin kasvoille, FREYR on hiljattain ilmoittanut vetäytyvänsä yhteistyöstä 24M:n kanssa, mikä viittaa siihen, että ala saattaa kääntyä yhä vahvemmin kuivaelektroditekniikan suuntaan.(Anonymous, 2024) Tämä on merkittävä kehityskulku, joka saattaa nopeuttaa kuivamenetelmien kehittymistä ja markkina-aseman vahvistumista.
Mitä seuraavaksi on luvassa?
Jos kuivaelektrodien valmistuksesta halutaan ottaa kaikki hyöty irti, seuraava looginen kehitysaskel on kuivaushuoneiden optimointi. Kuivaushuoneiden osuus tuotantolaitosten tilantarpeesta ja energiankulutuksesta on merkittävä, joten niiden vähentäminen ja tehostaminen tuo suuria kustannussäästöjä. Toisaalta koko tuotantoprosessin siirtäminen kuivaushuoneisiin voisi itse asiassa parantaa kennon käyttöikää, sillä herkät materiaalit suojataan paremmin kosteudelta ja epäpuhtauksilta. Tämä saavutettavan tasapainon merkitys – eli kuivaushuoneiden tehokkuuden maksimointi samalla kun otetaan mukaan kriittiset tuotantovaiheet – on tulevaisuuden kilpailukyvyn kannalta ratkaiseva.
Yksi haaste on minimoida kuivaushuoneiden koko kuitenkaan uhraamatta suojaa, jota ne tarjoavat erityisesti herkille materiaaleille, kuten aktiivimateriaaleille ja elektrolyyteille. Jos tämä onnistutaan ratkaisemaan, todennäköisesti saavutetaan sekä kustannussäästöjä että pidempi kennojen elinikä. Tavoitteena onkin luoda tuotantoprosessi, joka on mahdollisimman tilatehokas ja energiapihi, mutta joka samalla tukee parasta mahdollista kennojen kestävyyttä.
Katse vielä kauemmas tulevaisuuteen
Yksi alan kiinnostavimmista tulevaisuuden tavoitteista on muodostusvaiheen (eng. formating) eliminointi. Tämä prosessi on kallis ja aikaa vievä ja on usein pullonkaula ennen kuin kennot voivat lähteä tehtaalta. Muodostusvaiheessa anodille muodostuu elektrolyytin hajoamisesta johtuva SEI-kerros (solid electrolyte interphase). Ilman SEI:tä akku ei toimisi ollenkaan, koska elektrolyyttiä jatkuvasti hajoaisi anodilla. SEI-kerroksen vakaus on yksi isoimpia syitä, mikä määrittää miten pitkäikäinen akkukenno on. SEI on kuitenkin myös suurin syypää akkukennojen kulumiselle. Oikein akkukennon kaksiteräinen miekka.
SEI kerroksen pystyy kumminkin tekemään myös keinotekoisesti kemiallisesti, joka on oma valtava tutkimusalansa.(Verma ym., 2010) Keinotekoisen SEI-kerroksen luominen vaatisi erittäin tarkkaa kontrollia. SEI:n muodostaminen keinotekoisesti on kuitenkin teknisesti erittäin vaativaa, sillä se vaatii SEI:n täydellistä ymmärrystä sekä elektrolyytin ja anodimateriaalin täydellistä hallintaa. Tähän suuntaan ollaan kumminkin pikkuhiljaa menossa. Nykyiset tutkimukset osoittavat kuitenkin, että katodimateriaalin kapasiteettilisäaineet, ovat erittäin tehokas tapa pidentää kennojen elinikää. Tämä on jo askel oikeaan suuntaan, ja jos kehitys jatkuu tällä tiellä, SEI:n keinotekoinen muodostus voisi olla seuraava suuri innovaatio akkuteollisuudessa.
Keinotekoisen SEI-kerroksen luominen hallitusti voisi poistaa muodostusvaiheen ja siten edelleen laskea valmistuskustannuksia sekä parantaa kennon elinikää. Mutta tietenkin tässä osaksi korvattaisiin toinen prosessiaskel toisella, mutta koska muodostuminen on myös valtava pullonkaula akkujen tuotannossa, kokonaiskuvassa tässä pitäisi olla järkeä.
Kestävä ja tehokas akkutuotanto
Akkuteollisuus kehittyy nyt nopeammin kuin koskaan ennen. Kuivaelektrodi-menetelmien kaltaiset innovaatiot ovat esimerkkejä siitä, kuinka teknologian kehittyminen voi vähentää kustannuksia, parantaa tuotannon tehokkuutta ja tehdä prosessista ympäristöystävällisempää. Samalla, kun nämä edistysaskeleet vievät alaa kohti kustannustehokkaampaa ja kestävämpää tuotantoa, ne antavat myös signaalin siitä, että akkutuotanto voi olla vieläkin halvempaa, joka on valtava virstanpylväs kestävän energiainfrastruktuurin rakentamisessa.
Juho Heiska
TkT, tutkimus- ja kehittämispäällikkö
SeAMK
Kirjoittaja on väitellyt akkututkimuksen alalta ja on toiminut sen jälkeen energiatekniikan yliopettajana VAMKissa. Tällä hetkellä hän toimii SeAMKissa digitaalisuus ja älykkäät teknologiat -tiimissä tutkimus- ja kehittämispäällikkönä. Hänen yhtenä asiantuntijuusalueenaan on energiatehokkuus.
Viitteet
Anonymous. (11.9.2024). FREYR Battery Ends Licensing Agreements with 24M Technologies – TipRanks.com. TipRanks Financial. https://www.tipranks.com/news/company-announcements/freyr-battery-ends-licensing-agreements-with-24m-technologies
Giesige, J. (ohjaaja). (7.8.2024). Dry Cathode Finally Solved! What was the delay? // Tesla Q2 Battery Report [Youtube]. https://www.youtube.com/watch?v=s1XWNPgYOKs
(Infographics #3) Battery Making at a Glance – Battery LAB. (14.6.2023). 배터리인사이드 | BATTERY INSIDE. https://inside.lgensol.com/en/2023/06/infographics-3-battery-making-at-a-glance/
Liu, Y., Zhang, R., Wang, J. & Wang, Y. (2021). Current and future lithium-ion battery manufacturing. iScience, 24(4), 102332. https://doi.org/10.1016/j.isci.2021.102332
Revolutionising battery production: how dry electrode manufacturing promises to cut costs. (1.11.2024). Benchmark Source. https://source.benchmarkminerals.com/article/revolutionising-battery-production-how-dry-electrode-manufacturing-promises-to-cut-costs
Verma, P., Maire, P. & Novák, P. (2010). A review of the features and analyses of the solid electrolyte interphase in Li-ion batteries. Electrochimica Acta, 55(22), 6332–6341. https://doi.org/10.1016/j.electacta.2010.05.072